
BRICK BUDDY
January - May 2019
PROJECT OVERVIEW
The Story:
For this company sponsored capstone project, the professors decided that the theme would be "Safety." However, safety is not limited to just physical safety but also potentially psychological safety. My team and I wanted to figure out how to increase the safety in theaters. At the end we needed a prototype and presentation on why our final solution satisfies a great need.
My Impact:
My main responsibilities in this project were conducting Interviews, leading and justifying Data Analysis, researching Human Factors, building Lo-Fidelity Prototypes, and writing up the Failure-Mode-Analysis.
PROCESS
Execution: What I either participated in or I took sole ownership of for this project
Objective: The goals or purpose of what I executed
Result: What actually happened from the Execution
OBSERVATIONS
Execution: Went to theater productions to watch the behind-the-scenes of a show as well as watch the preparations before the actual showcase
Objective: Watch the process of a theater production as well as witness some potential pain points that need our attention
Result: Noticed how the rigging system in theaters are manual and requires a stagehand, two stories above the stage to load counter-weights by hand into the system to put the mechanical system in equilibrium when hoisting curtains, speakers, and lighting equipment
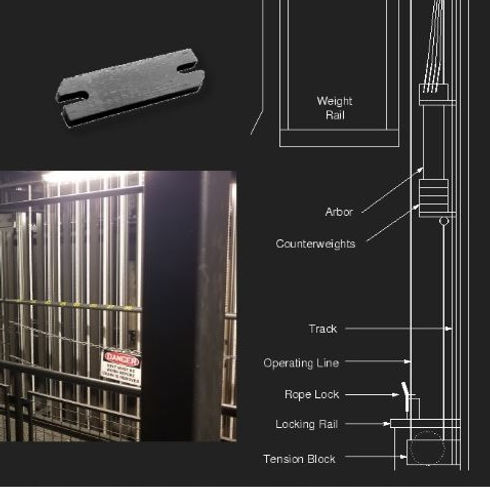
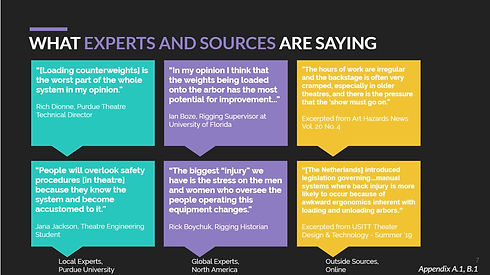
INTERVIEWS
Execution: Talk with college student stage hands, stage managers, a “rigging historian,” and theater professors about the rigging system in theaters
Objective: Learn from their experience how to run a rigging system and what are some dangers that can cause a risk to security
Result: Because everything is done by hand, two stories above the stage, this manual rigging system causes chronic strain on the human body as well as mental stress to everyone involved in case someone drops a counterweight or the rigging system is not set in equilibrium
JOURNEY MAPPING
Execution: Based on the interviews map out the process that goes into hoisting up lighting equipment up the rigging system
Objective: Figure out what part of the rigging system requires the most attention for a solution
Result: Found that the majority of pain points were in the loading and unloading counterweights portion of the rigging system

SECONDARY RESEARCH
Execution: Look up safety protocols and codes (OSHA) that people need to adhere to as well as articles of instances of failures of the rigging system in theaters
Objective: Learn all possible things that can go wrong if a rigging system is not worked correctly and why there doesn’t seem to be any statistics of instances of injuries or deaths in the theater
Result: Unlike most other systems that show such statistics, theater injuries and deaths are not recorded anymore. When I asked the experts about this missing statistic, they told me that it does not exist because the theater production would rather “sweep the issue under the rug” if it means that “the show can go on.”

DATA ANALYSIS & SYNTHESIS
Execution: Take all the interviews between everyone we talked to and categories quotes based on specific frustrations with the rigging system
Objective: Understand why there hasn’t anything been done despite all the clear security risks and issues pointing to loading and unloading counterweights two stories above the stage
Result: Culture of the art comes into play. Because theater is art, anything contributing to theater is also art and pride to be a part of. The current rigging system is the same manual rigging system since the 1800s (according to the rigging historian), and, therefore, changing the rigging system to automatic without manual handling of the counterweight takes away the tradition, art, and history of the theater. Additionally, changing to an automatic rigging system is too expensive for the majority of theatres to afford.
DEFINING PERSONAS
Execution: Creating personas of all range of stagehand users
Objective: Have a clear representative of who we are trying to serve
Result: Three personas of three different groupings of users all of who we want to satisfy
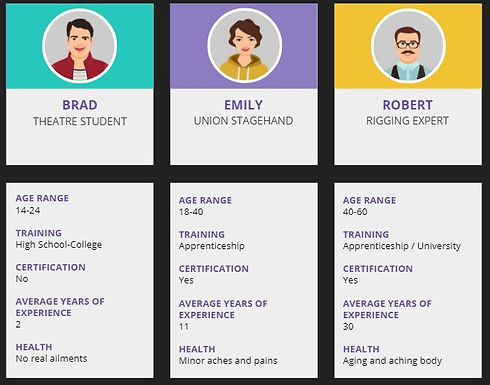

DEFINING DESIGN HEURISTICS
Execution: Define specific criteria for the final solution
Objective: The final solution must satisfy this problem by adhering to both the stage-hand’s needs as well as theater safety codes
Result: Justify eight specific criteria that the final solution must satisfy with prioritizing process effectiveness (increase efficiency of the rigging system), non-intrusive (Doesn’t interfere with the original fly system process, respects the trade of rigging), and cost-effective (Affordable for specific product, ease of acquirement, and high product life expectancy)
BRAINSTORMING
Execution: Brainstorm countless drawings, descriptions, and sketches on post-its before building very lo-fidelity prototypes made from craft supplies
Objective: Get out as many ideas as well as many variations of ideas as possible on paper and as models
Result: Found a lot of repeats in design and found three top ideas to decide between

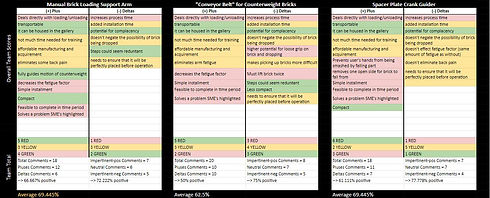
DECIDING ON ONE PROTOTYPE
Execution: Utilize our design heuristics as criteria for a decision matrix
Objective: Based on the priorities of the design heuristics that satisfy the needs of the stagehands and are backed up by our secondary research, calculate which of the three top ideas should be pursued as our main prototype
Result: Decide to pursue an extendable arm that grips a counterweight with a magnet out onto the arbor without exerting strain on the stagehand’s body
ITERATING
Execution: Take our top idea and make as many lo-fidelity prototypes as possible out of craft supplies
Objective: See through models how to continue to make the prototype better
Result: Came up with more than twenty variations of the same design, but discover with statics calculations, theater safety code, and testing one variation that best fits satisfying the problem

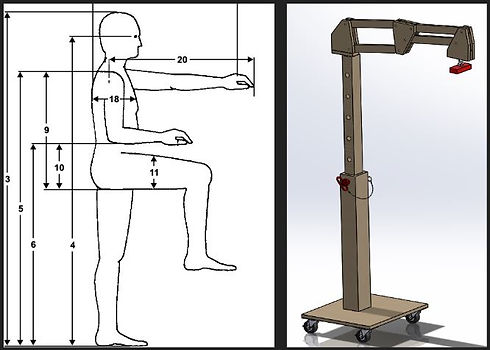
HUMAN FACTORS
Execution: Utilize the NASA task index for the 95% of both men and women in terms of arm length and extension
Objective: Because the ratio of stagehands between men and women are roughly fifty-fifty, I needed to research what measurements the final product needs to be to accommodate for both men and women
Result: Found an average and range of the height and arm length and extension without physical stress so that my teammates can create CAD drawings and build a physical model
USER TESTING
Execution: Take the made prototype to a theater and had a stagehand practice using it with the rigging system
Objective: Observe the user using the prototype and receive feedback on how to improve the prototype
Result: Learned that stagehands would still be hesitant to use the prototype, but because it is easy to use and learn how to use, with time more stagehands will want to use it for their own safety


FAILURE MODE ANALYSIS
Execution: Think of all possible ways this design can fail and rank the severity of failure backed up by feedback from users as well as secondary research
Objective: Ensure that every possible failure is accounted for and measures are implemented to counteract those failures
Result: Found that the only main way that this design can fail is if users are being reckless and “roughhousing” with it (i.e. riding it like a shopping cart)
FINAL SOLUTION
The Brick Buddy aims to tackle the problems of back strain and fatigue suffered by the counterweight loader with secondary goals to mitigate the issues that may be caused by fatigue. The bending suspension arm design allows for both compact storage as well as a loading process fully guided by the loader with his/her hands remaining on the brick. It features an adjustable mount to allow for loading at various heights by simply pulling out the pin and lifting the lightweight arm to the desired height and replacing the pin. The square base is compact to maintain OSHA standards for walking spaces on a suspended catwalk. The caster wheels allow for easy movement up and down the gallery and can lock when in the desired position. The connection point of the magnet allows for easy connection without having to remove hands from the brick and for fully guided motion by the loader.
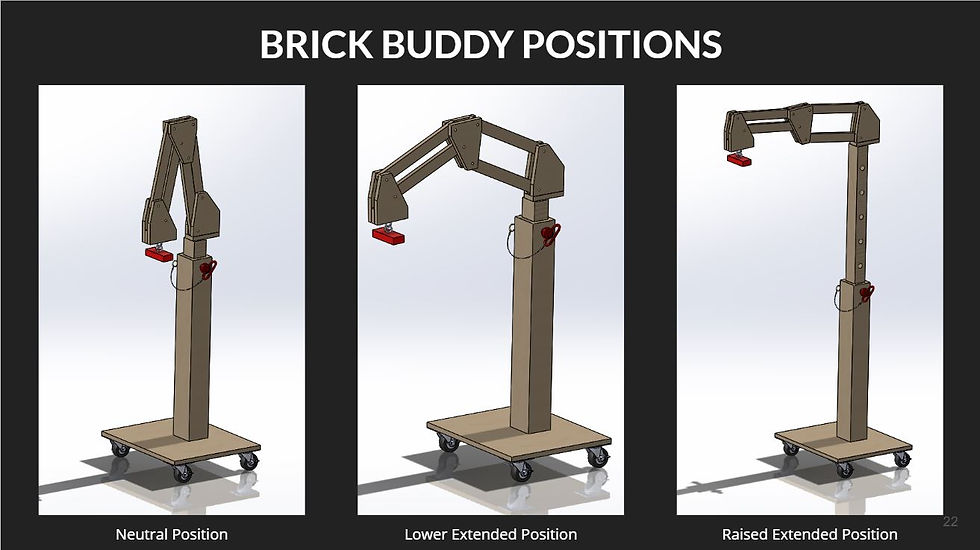
SKILLS
Justification
Human Factors
Design Research
TAKEAWAYS
Sometimes there is a clear and obvious problem even when there is no “proof” to back it up. In the case of this project, the fact that there were no clear statistics or data backing up that this was a real problem made us rely heavily on qualitative data and analysis to provide justification for the need to address this problem. Additionally, I learned that every single decision in the design process needs to be justified and backed up with data and research so that every decision made is a clear decision validated for credibility of the final solution.